tomfly
The only thing left should be foot prints.
After being out bid on many Bamboo rods on ebay. I was finaly triumphant and recieved the rod today. I was working on $50.00 budget. You may ask; why so cheep? This is the first Rod that I am attempting to do. So if I destroy the rod although disappointing it would be. It would not hurt so much economicly. I have full undersatanding of the daunting task that I am about to partake in. The rod I bought is a Shakespeare Bamboo Fly Rod model A1305B-9'. Not an overwhelming sought after fly rod. But I think it will be a fun first project.
I am setting up this blog so my freinds NEFF can share in the chronological redo or destruction of this rod. I want to share my achevements and my failures in the learning process. I am starting out with absolutely no tools to do this with. But I will address it when they are needed. I am letting you all know now I am not doing a restoration project. I have my owne vision for the rod. Weather I can obtain my goal still has yet to be determined. Any feed back or constructive criticism durring the process would be appreacheated. I am attaching some pictures as the rod as it looked on ebay.
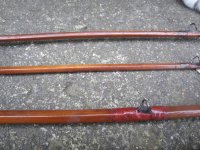
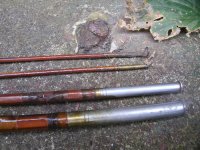
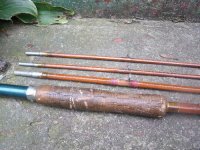
I am setting up this blog so my freinds NEFF can share in the chronological redo or destruction of this rod. I want to share my achevements and my failures in the learning process. I am starting out with absolutely no tools to do this with. But I will address it when they are needed. I am letting you all know now I am not doing a restoration project. I have my owne vision for the rod. Weather I can obtain my goal still has yet to be determined. Any feed back or constructive criticism durring the process would be appreacheated. I am attaching some pictures as the rod as it looked on ebay.
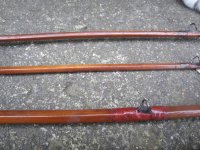
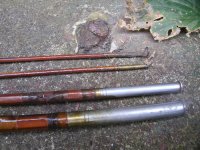
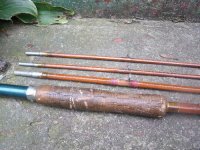